Rail Gas Pressure Welding Apparatus
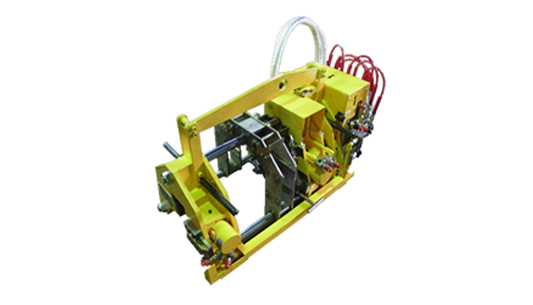
Reliability, workability, and economy are our strengths.
Rails have been made longer to prevent running noises, to improve riding comfort and to reduce rail track maintenance cost due to higher train speed.
Gas pressure welding is mostly mechanically accomplished. Therefore, joining strength is even and highly reliable.
The same strength can be obtained by either gas pressure welding or flash butt welding.
In this welding method, on-track welding as well as shop or field depot welding are available.
Characteristics
This apparatus is geared to obtain uniform weld quality.
Because burrs are cut off through extrusion while during high temperature right after gas pressure welding, when a defect such as weld flaw occurs in the weld joint, it is opened during extrusion for trimming and this is effective for quality control.
Weld Strength and Hardness
Because heating temperature is controlled below the steel melting point and no filler metal is used, weld strength is as high as that of the base metal.
The weld joint of the head hardened rail is softened due to welding heat.
However, a post - weld heat treatment device can be used to restore the hardness of the welded part as high as that of the base metal.
Workability
This apparatus is designed for compactness , lightweight and mobility to make on-track application possible, not to speak of shops or field depot welding.
Pressure welding efficiency with this apparatus is remarkably high.
Economy
Main consumables are oxygen, acetylene, fuel for the generator and grinding stones.
Cost per weld is far more economical than that of other welding methods even when amortization for machines and labor cost are considered.
Welding Method
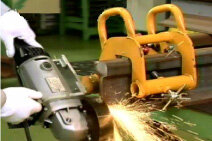
Rail End Surface Grinding
Grinding of the rail end surface is necessary for the rail gas pressure welding. After it squarely finishes it up with a special grinder, the cleaning agent washes the worked surface.
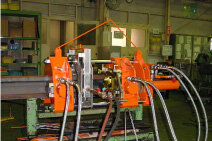
Setting of Pressure Welding Apparatus
The welding machine is set on the rail, and the alignment checked of the rail is can take place. Next, the welding condition is to bechecked.

In Process of Pressure Welding
The welding machine pressurizes and heats the butting part of all surroundings with a special burner by oxy-acetylene flames and both rails are joined.

Finish of Pressure Welding
After setting the trimmer, extinguish the fire of the burner and stop upsetting, release the clamp on the right side.
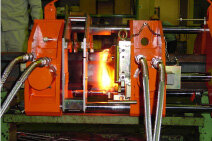
Trimming
Hot shear removal of the burr of the whole circumference with a trimmer.
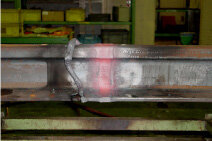
Welded Part Right After Pressure Welding
After trimming, the welder has to check the crack at the joint point. After grinding, penetrant test and magnetic particle test are examined
Specification
Model | Manual type | Semi-Auto type | ||
---|---|---|---|---|
TGP-5 | TGP-5-B | TGP-8-S2-T(C) | ||
Main Body | Clamping force | Max 230kN | Max 230kN | Max 230kN |
Upset force | Max 330kN | Max 330kN | Max 330kN | |
Size (mm) | L1,310×W550×H740 | L1,380×W570×H775 | L1,350×W570×H660 | |
※Carrying Weight | 230kg | 270kg | 290kg | |
※Working Weight | 300kg | 350kg | 360kg | |
Appearance | ![]() |
![]() |
![]() |
|
Hydraulic pump | Power supply | 1.5kW, 200/220V, 50/60Hz, 3-phase | 2kW, 200/220V60Hz,3-phase | |
Other than the above voltage can be manufactured. Please consult us. | ||||
Max. pressure | 70MPa | 70MPa | ||
Size (mm) | W600×D550×H850 | W600×D550×H850 | ||
Weight | 120kg | 135kg | ||
Appearance | ![]() |
![]() |
||
Operation unit | Operation method | Manual operation of hydraulic changeover valve | Touchscreen operation | |
Size (mm) | W725×D575×H700 | W201×D97×H230 | ||
Weight | 65kg | 1kg | ||
Appearance | ![]() |
![]() |
||
Operating environment | Temperature: 0 ℃ (-10℃) to 40℃, humidity: 20 to 85% RH, but no condensation. In ( ), cold district specification type:【TGP-8-S2-TC】 |
|||
Characteristic | ・Light weight type | ・Rigidity type ・Replaceable consumable parts |
・Hydraulic operation is automatic ・Welding record ・Automatic control of closure welding ・Hydraulic hose reduction |
※Carrying:at the carrying / without hydraulic equipments.
※Working:at the working / with hydraulic equipments.
DESIGN/PARTS may be changed without notice